|
※본 나사의 조임방법'예시는 주로 사용하는 방법의 예시에 대한 안내일 뿐이며, 본 내용을 기준으로 설계에 적용하여 발생하는 결과에 대해 저희 화인드아이는 일체의 책임이 없습니다.
일반적으로 많이 쓰이는 나사의 조임방법에는 "토크 값 제어방식"과 "조임 각도 제어방식"의 두 가지가 있다. 본 장에서는 각도제어 방식에 대해 알아 본다. (토크 값 제어방식은 나사의 조임토크 결정 ( Tightening torque )예시 참조바람) 조임 각도 제어방식(Angular tightening method)이란 나사를 조일 때 일정 토크값으로 1차 조임을 하고 다시 일정한 각도 만큼을 조이는 방식이다.
|
|
|
일반적으로 많이 쓰이는 나사의 조임방법에는 "토크 값 제어방식"과 "조임 각도 제어방식"의 두 가지가 있다. 본 장에서는 각도제어 방식에 대해 알아 본다. (토크 값 제어방식은 나사의 조임토크 결정 ( Tightening torque )예시 참조바람) 조임 각도 제어방식(Angular tightening method)이란 나사를 조일 때 일정 토크값으로 1차 조임을 하고 다시 일정한 각도 만큼을 조이는 방식이다. | |
|
각도제어 방식의 사용 목적 |
 | |
|
1. 각각의 볼트에 걸리는 체결력의 산포를 최소화 하기위해 사용한다. |
|
토크렌치(torque wrench)를 이용하여 나사를 조이는 토크제어 방식의 경우 토크값의 상한치와 하한치의 범위를 갖을 수 밖에 없으며, 이로 인해 볼트에 걸리는 실제 축력의 산포는 훨씬 커지게 된다. ('그림 1.조임토크와 축력' 참조바람) 동일한 토크값으로 조였다손 치더라도 나사산의 정밀도나 표면 거칠기, 볼트좌면의 상태등에 따라 마찰력이 달라서 실제 볼트가 조여짐으로써 갖게 되는 볼트의 체결력에는 상당한 차이를 보이는 것이 일반적이다.특히 탄성역 내에서 조여지는 경우는 그래프의 기울기가 커서 축력의 산포는 더욱 커지게 된다. 그러나, 마찰력의 영향이 최소인 착좌점까지 조인후 일정한 각도로 재조임을 할 경우 마찰력에 의한 여러 가지 영향이 배제된 상태로 조여지므로 실제 축력의 차이가 작아지게 된다. 조임공구에 각도기가 달려 있어야 하므로 조임 작업에 불편이 따르지만, 풀림방지를 위한 균일한 조임력을 얻고 싶은 곳에는 추천할 만한 방식이다. | |
|
|
【 그림1. 조임토크와 축력 】 |
| |
|
| |
|
2. 볼트가 갖고 있는 강도를 최대한 사용하기 위함이다. |
|
위의 (그림1. 조임토크와 축력)의 그래프에서 보듯이 토크로 조일 경우 그 값이 조금만 넘어가면 바로 볼트의 파손이 생기게 된다. 이는 항복점을 지나면 토크값이 증가되지 않으면서 조여지다가 결국은 파손에 이르기 때문이다. 따라서, 파손의 위험으로부터 어느 정도 안전한 작업을 하기 위해 탄성역을 넘지 않는 한도에서 조임토크의 상한치를 설정하는 것이 일반적이었다. 이러한 이유로 인해 실제로 사용되는 축력은 볼트강도의 50 ~ 70% 정도만이 사용되었다. 아래 (그림2. 조임각도와 축력)은 볼트를 조이면서 파손될 때까지 조여진 각도별 축력을 그린 것이다. 항복점을 지나 최대 축력(Fm)점까지 각도의 범위가 상당히 넓은 것을 알 수 있다. 또한, 파손점까지는 상당히 여유가 있음을 알 수 있다. 이 원리를 이용하여 착좌점까지는 토크값으로 조인후 각도로서 재조임을 하는 2단계 조임방법을 사용하면, 볼트가 갖고 있는 최대 강도까지 사용할 수 있어 동일한 축력을 얻기 위해서는 호칭경이 작은 볼트를 사용할 수 있다. 혹은 동일 호칭경에 강도등급이 한등급 낮은 볼트를 사용할 수도 있다. 여러개의 볼트를 사용하는 경우에는 볼트의 숫자를 줄일 수도 있다. |
적용예) M8x1.25x50, 강도등급 10.9 인 볼트의 조임 토크 | |
|
|
|
- 토크조임 방식의 경우 |
: 토크 상한치 = 38N.m, 토크 하한치 = 33N.m |
|
( 파손 토크 = 41N.m ) |
- 각도조임 방식의 경우 |
: 25N.m + 30° | | |
|
|
|
|
|
【 그림2. 조임각도와 축력 】 |
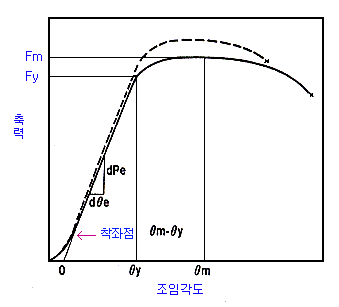 | | |
|
|
|
 |
참고 1. 착좌점이란? | |
|
(그림2. 조임각도와 축력)에서 보면, 초기에 나사를 조여도 탄성영역 임에도 불구하고 축력이 조임각도에 비례하여 상승되지 않는 구간이 존재함을 알 수 있다. 이는 나사의 미끄럼이나 표면의 자리잡음 효과등에 기인된다. 이 미끄럼이 끝나고 피체 결물이 서로 밀착되는 점(탄성영역으로 진입되는 점)을 착좌점(snug point)이라 하며, 이때의 토크값을 착좌토크(snug torque)라고 한다. |
 |
참고 2. 탄성역 ( 탄성영역 )이란? | |
|
(그림2. 조임각도와 축력)에서 조임각도 θy 까지는 조여지는 각도에 따라 축력의 증가가 거의 직선으로 이루어 지며, 이 구간 내에서는 가했던 힘을 제거하면 원래 모습으로 되돌아 오게 되므로 이 영역을 탄성역이라고 부른다. |
 |
참고 3. 소성역 ( 소성영역 )이란? | |
|
(그림2. 조임각도와 축력)에서 탄성역을 지나면 가했던 힘을 제거해도 원래의 모습으로 돌아오지 않고 어느 정도 나사의 길이가 늘어나 영구 변형량을 보이게 되며 이러한 영구변형은 소성변형이므로 이 영역을 소성역이라고 부른다. |
 |
참고 4. 항복점이란? | |
|
(그림2. 조임각도와 축력)에서 θy를 기준으로 왼쪽은 탄성역, 오른쪽은 소성역이 된다. 이러한 타성역과 소성역의 경계점을 항복점이라고 부른다. | |
|
|
|
각도제어 방식의 적용시 주의할 점 |
 | |
|
1. 나사의 최대 체결력 사용범위 결정에 신중해야 한다. |
|
탄성영역까지만 사용할 것인지, 소성영역까지 사용할 것인지 신중히 검토해야 한다. 볼트의 갯수나 사용위치 등에 대한 제약조건이 별로 없는 부위에 사용하는 볼트라면 탄성영역까지만 사용할 것을 권장한다. 하지만, 엔진등과 같이 협소한 장소에서 제한된 수량을 볼트를 사용해야 할 경우에는 소성역까지 사용하는 것이 효과적인 대안이 될 수 있다. | |
|
|
|
2. 나사의 품질 및 내구성 확인에 신중해야 한다. |
|
볼트의 재질이나 열처리 등에 따라 (그림2. 조임각도와 축력)과 같은 곡선그래프의 기울기는 계속해서 바뀌게 된다. 따라서, 제품의 품질 산포가 어느 정도 인지 확신이 없다면 탄성역 안에서 사용하는 것이 안전하다. |
소성역 체결을 위한 볼트의 경우 |
|
항복점의 산포가 적은 재료의 볼트를 선정한다
항복점에 이르는 탄성역의 그래프 기울기(그림 2의 dPe/dθe)가 작아 항복점까지의 조임각도(θy)가 큰 제품을 선정한다.
항복점에서 최대축력(θm)에 도달하는 각도가 큰 제품(연신율이 좋은 것)을 선정한다.
열처리의 관리가 잘 이루어질 수 있는 믿을 수 있는 회사의 제품을 선정한다.
볼트가 인장력을 받으므로 늘어날 수 있는 여유 나사부의 확보가 반드시 필요하다. 전산나사를 사용하는 것이 가장 좋다. 하지만, 불필요하게 나사부가 너무 길어지는 경우라면 유효경 부분나사를 사용하면 유효경 부분에서 인장력을 받아 늘어나므로 좋다. 그러나, 결합물의 위치등을 위해 공칭경 나사를 사용하고자 할 경우에는 조여진 후 남는 나사산의 수를 약 5산 이상을 남기는 것이 좋다. 이 부위가 너무 짧으면, 인장이 집중되어 파손의 원인이 될 수 있다.
부분나사를 사용할 경우 불완전 나사부에서 단면적을 감소시키는 효과(notch effect)를 갖어 올 수도 있으므로 이 부위의 형상에 특히 신경을 써야 한다. |
소성역 체결을 할 경우 볼트의 내구성을 신중히 확인해야 한다. 특히, 진동 및 외력이 작용하는 곳에 사용된다면 내력시험(creep test), 내구 수명 확인 시험등을 거치는 것이 좋다. | |